top of page
WL

Form Generation
Parametric design, 3D printing, waffle structure construction, laser cutting
In this module, the focus was on form discovery and experimentation with subtractive and additive geometry using Rhino and Grasshopper.
​
Selected geometries are then fabricated using 3D printing as well as laser cutting.


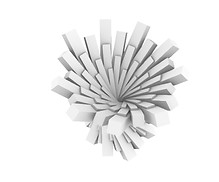


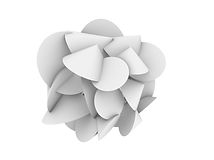
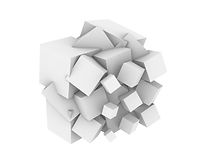
First, there were iterations...

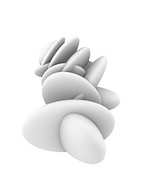
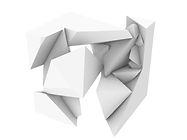
after iterations...
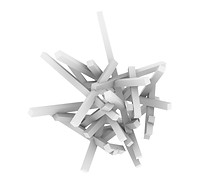

after iterations...

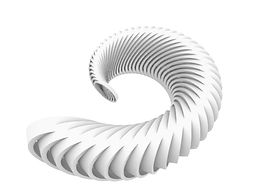
after iterations.
Aggregation and Subtraction
after iterations...
after iterations...
3D Printing Files



Then, these three geometries are selected to be 3D printed. Here, rafts and breakaway supports are turned on to allow for a higher precision print.
Scale Tests

At the scale of an interactive sculpture the crystal-like cantilever offers sheltered spaces underneath. The opening becomes a portal which people can climb through, or communicate to people on the other side. The extracted shape from a cube adds an element of asymmetry into the highly regular, rotated rectangular prisms.
Observed from the outside, this design is merely a cube. Yet the interior space is highly dynamic and intricate. At this scale,the geometry can be inhabited - steps and sheltered seating areas. The rhythm created by the spiralling forms is perceptible by visitors both visually and in a tactile manner as they move through the pavilion.
At the scale of a pavilion, the underside details of the cantilevers to be seen to heighten the drama of the main fan-like form.The aperture here is a visual device to draw people into the enclosed spaces inside the pavilion. The Magnitude of point attractor was key in creating a sense of dynamicism in this design.

Nested Lasercutting File
Two further geometries were chosen to be lasercut using orthogonal and radia waffle techniques.
​
Laying out the lasercut shapes on the template required much care to ensure that spacing between cut lines are greater than 2mm, else it would burn. Etching is used to label each geometry for ease of assembly. One edge of each geometry is also etched to avoid them falling out after being cut. They can then be released with a knife later during assembly for clean and efficient workflow.
Waffle Geometry Scale Tests

Translating the original geometry into a waffle structure creates functional opportunities and affordances such as storage, shelter and stepped seating. The rotated form now can be adapted as a sculptural library where books can be placed on differently sized shelves and people can also sit on the stepped platforms on the other side of the geometry. These affordances result from the nature of the orthogonal waffle and also my revised script of exponential distances for X and Y sectioning.
This geometry at the scale of a pavilion would be able to accommodate a range of artistic performances. The radial panels not only draw the audience’s attention to the performers, they can also be designed to perform acoustic functions. The idea of the portal now is more nuanced as it is layered with the performance to further transport the viewer to another realm.
Process Journal
bottom of page